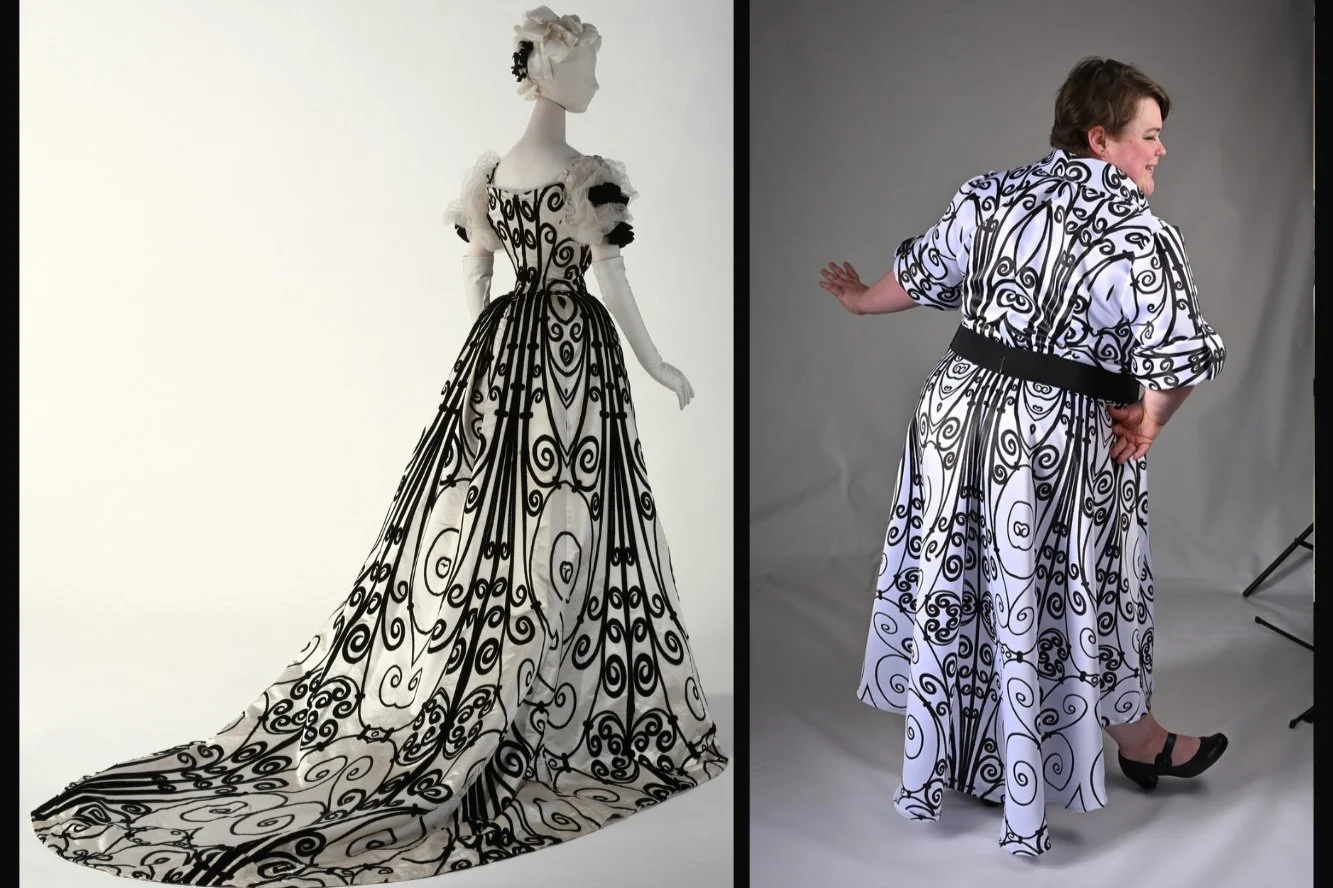
Engineered Textile Design
Ironwork Sundress
This garment is inspired by the aptly nicknamed Ironwork Gown from the House of Worth, circa 1898-1900. The garment is housed at the Met’s Costume Institute. I’ve loved this gown ever since I started pursuing costume design, and wanted to find a way to make a garment inspired by it. When I first learned about engineered textiles, I realized I could use this technique to create a modern take on this historical classic.
From my research in the Met’s archive, I found they also owned a sister dress with the same pattern, and there were flat archival photos of this variant. I attempted to perform a digital isolation of the existing pattern, but the fading of the original garment made this come out splotchy, so I opted to redraw a portion of the pattern by hand, then mirror and flip this drawing to create a textile pattern tile.
Historical Inspiration
Digital Textile Design and Patterning
I found a handful of digital patterns in my collection that I chose to use for this project. The sundress had the perfect top half for the idea I had in mind, but I chose to use a high-low skirt pattern to emulate the feeling of the train on the original ball gown.
I first assembled the printing pages for both patterns in Photoshop, and ensured the pattern pieces had scaled correctly using the inch ruler tool. I then retraced the edges of each pattern piece, to ensure they were not pixelated after being enhanced to the correct size.
Once the setup was complete, I used the pattern tile I had drawn and placed them over the pattern pieces. By placing the pattern over the individual pieces instead of ordering a roll of fabric, I was able to ensure all pattern matching was accurate and complete before the fabric even arrived. On the sections that called for darts, I moved the pattern around the dart and manually filled in the gaps between edges, to prevent any non-patterned gaps in case the garment later needed to be let out.
As I didn’t have a local method to print the fabric, I printed out segments of the patterned pieces on printer paper and assembled them into a half-scale mockup. Once I was sure my patterns were matching and there were no awkward placement issues, I rearranged the pieces on a grain line and prepared the file for printing.
Final Results
I sent the final file to Contrado for custom fabric printing and shipping. I was thrilled with their duchess satin option, as it seemed like a perfect fusion of the historical garment’s elegance and the modern garment’s chic edge.
Since all the measuring and pattern-matching had been done digitally, I was able to save over a week’s worth of work once I received the garment. I spent approximately a day and a half serging and assembling the dress, then a day to fit and make minor adjustments.
The dress turned out perfectly! I’m happy to have a finished version of the dress, as I feel it demonstrates that historical garments can be translated to plus size bodies and look fabulous! I’ve shown the finished garment at the opening night of La Belle et la Bete (Spring 2025) and Design Showcase West 2025, and I’m planning to show it frequently in the future!